MODEL: AFS – ADVANCED FILTRATION SYSTEMS
FILTRATION SERIES
ITM holds over 30 patented machine designs
SUPERIOR & EFFICIENT FILTRATION OF PARTICLES AS SMALL AS 3 MICRONS
ADVANCED FILTRATION SYSTEM
As a manufacturer of precision grinding machines, ITM knows the importance of a precise and dependable coolant supply. After a long period of research and testing, ITM selected diatomaceous earth (DE) as the filter media for its line of automatic coolant delivery and filtration system. DE consists of skeletal remains of microscopic aquatic organisms with size varying from 10-200 microns in diameter. Compared to conventional filter media with plain and even surface, DE particles have a very large surface area in relation to their overall size. DE coated candles in ITM filter systems enable filtration of particles as small as 3 microns versus 20 microns with conventional system. DE is being used as a filter media in the beverage and water cleaning industries having proven its superiority and safety.
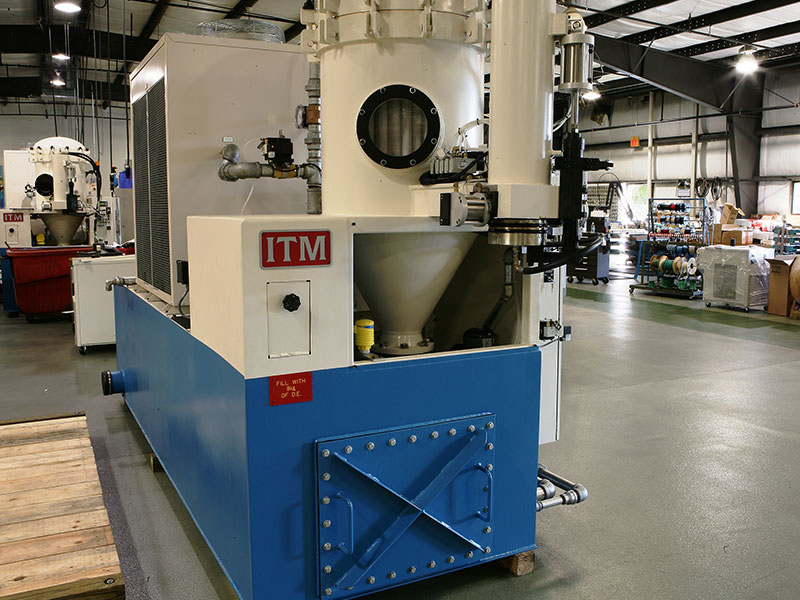
AFS-8-20 unit with sludge dryer
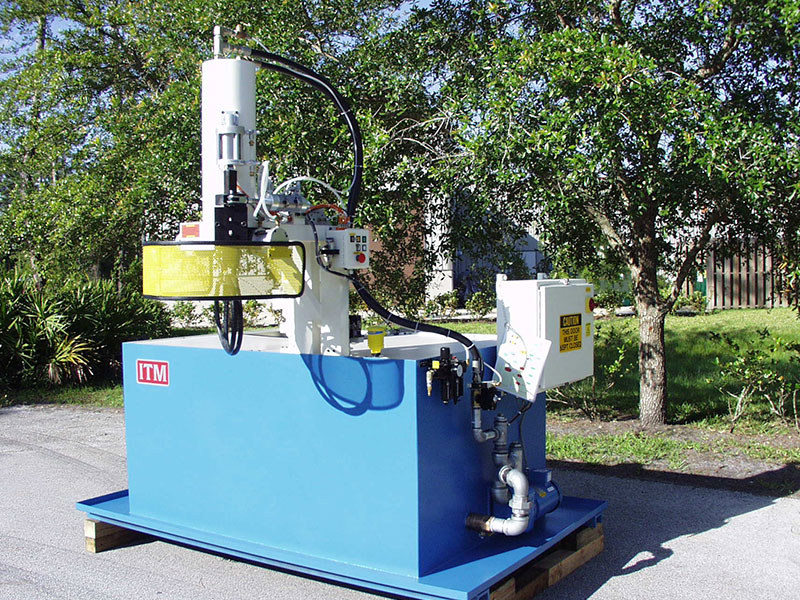
Independent pneumatic sludge dryer
HOW IT WORKS
In the filtering process, grinding residue collects on the outer surface of the coated candles as the coolant is drawn through them and into the clean coolant reservoir. The resulting flow rate of the filter will be reduced as this residue collects. Using a built-in flow meter, the flow rate can be monitored, and the filter residue can be dumped when a pre-determined rate is reached. The candles in the dome will be back flushed with clean coolant during this dumping cycle to assure that all residue and used DE are removed from the candles. The candles are then recoated with DE, and a new filter cycle is started, while the grinding sludge is automatically separated and dried by the fully automated sludge dryer unit. After the filter has been dumped, dirty oil with sludge is pumped into this dryer unit. The oil is separated from the sludge and returned to the cleaning cycle by pressing it out with up to 90PSI of air pressure. The remaining cake of sludge is then dried and automatically dumped into a disposal bin, or the sludge can be further reduced in volume with ITM’s optional sludge compactor for additional waste disposal cost savings.
Optionally, a variety of quality high pressure coolant pumps with pressures up to 1000PSI are available. Multiple pumps can be attached to each AFS including pumps utilized for “wheel scrubbing”. The integrated chiller unit maintains coolant temperature within 1°F, improving the surface finish of the tools and the tolerance holding capabilities of the grinding machine.
For further information regarding ITM’s Advanced Filtration System, contact us at (386) 585-8166
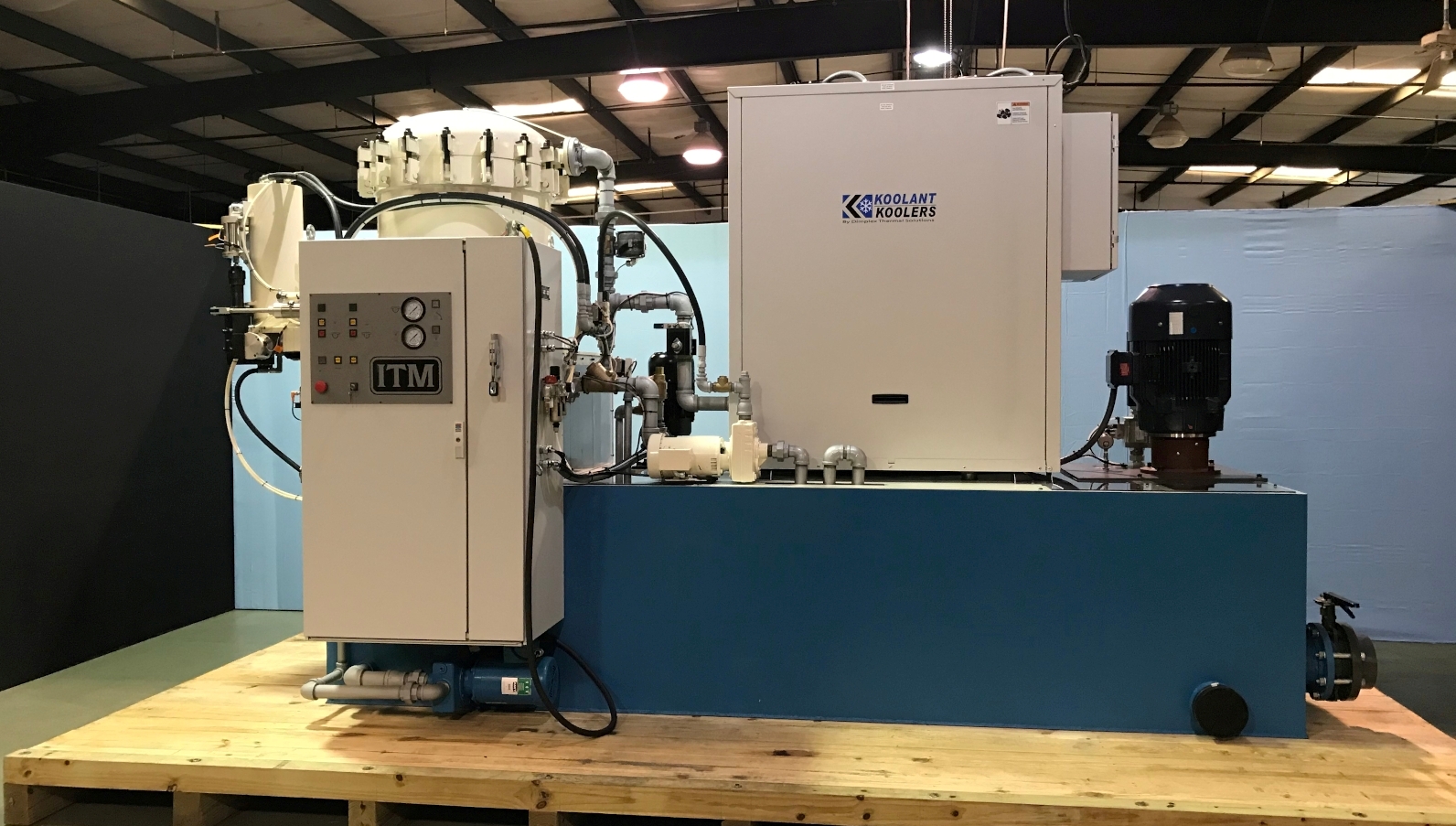
ADVANCED FILTRATION ACCESSORIES
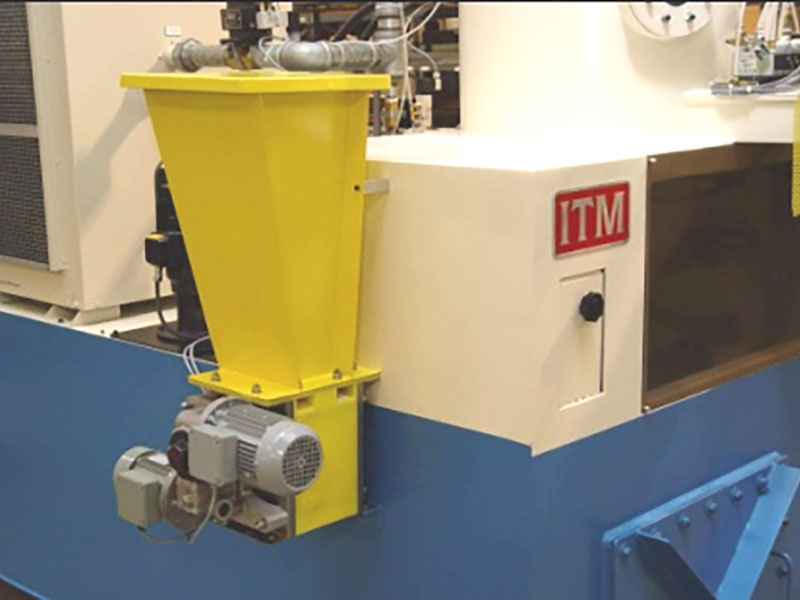
Chemical mixer option for 24/7 unmanned operation
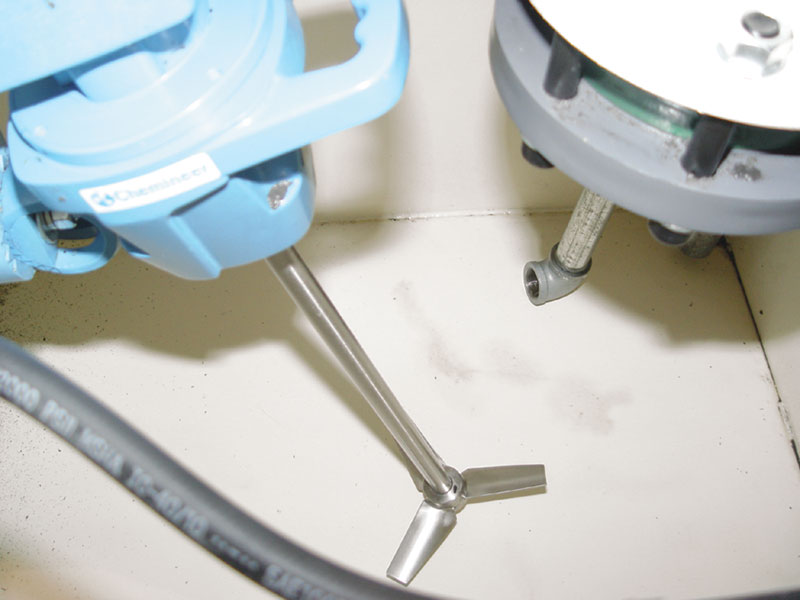
Standard sludge mixer for the dryer
COMPLETELY AUTOMATED FILTRATION FOR 24/7 OPERATIONS
CLEANING CYCLES
Grinding swarf will collect on the outer surface of the coated candles as the coolant is drawn through the candles to the clean coolant reservoir. The flow rate of the filter will be reduced as the swarf collects on the outside of the candles. Using the built-in flow meter, the filter can be dumped once a pre-determined flow rate is reached. The candles in the dome will be back flushed with clean coolant during this dumping cycle to assure that all the grinding swarf is removed from the candles. The swarf is prevented from settling in the holding tank with the use of an electric motor driven agitator. A removable panel allows for easy access to the sludge tank. An automatic hopper is used to deliver the correct amount of DE during the filter candle coating cycle.
AUTOMATIC SLUDGE DRYING CYCLE
ITM filters are equipped with a fully automatic sludge dryer in place of a standard vacuum system, to separate oil from the grinding sludge. After the filter has been dumped, the dirty oil with sludge is pumped into the dryer unit. The oil is separated
and returned to the cleaning cycle by pressing it out of the sludge with the use of up to 6 bar (90 psi) air pressure. The cake, which is left, is then dried and automatically dumped into a disposal bin or further compressed by an automatic compactor.
OPERATOR INTERFACE
The AFS 8-20 has an operator interface that is easy to use. The operation of the filtration system is by a Programmable Logic Controller (PLC). Variables such as filter flush time and sludge dryer drying time can be set directly on the LCD display and processed by the PLC.